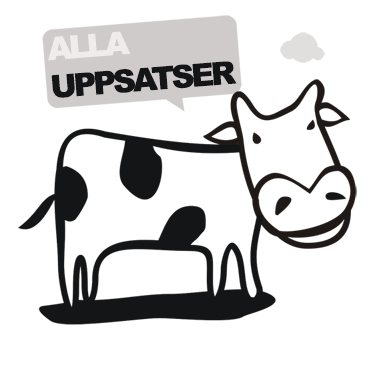
Sökresultat:
3462 Uppsatser om Production Flow - Sida 1 av 231
Utformning av ett materialflödessystem anpassat för HSP-Gripens produktion
Like many small-time companies there is a need to improve the flow of materials at HSP-Gripen AB. The company develops and manufactures hydraulic-powered grapples for the machine- and forest industry. By mapping the material flow in the current production and gathering necessary data, suggestions on how different parts of the production could be controlled is presented in this dissertation. This has been achieved by the study of relevant scientific literature. The suggested ways of controlling the production consist of 2-bin systems, hybrid material flow system as well as a cyclic product-planning.
Effektivisering av produktionsgrupp : Improving the efficiency of a production group
The report is about efficiency of a current production group where there is no clear Production Flow and there are some buffers between the operations. The efficiency is done with the help of a tool that is calledWork process of flow production which is used by Atlas Copco CTO. The most obviously results are that the lead time drops from 25 hours to 425 minutes and that the balancing loss decreases from 85 % to 8 %. The report focus on decreasing transports, decreasing buffers, more reliability in lead time and quality. And a more stimulating labour content for the workers is another result..
Till framtida utvecklare
The report is about efficiency of a current production group where there is no clear Production Flow and there are some buffers between the operations. The efficiency is done with the help of a tool that is calledWork process of flow production which is used by Atlas Copco CTO. The most obviously results are that the lead time drops from 25 hours to 425 minutes and that the balancing loss decreases from 85 % to 8 %. The report focus on decreasing transports, decreasing buffers, more reliability in lead time and quality. And a more stimulating labour content for the workers is another result..
Reducering av ledtid genom en värdeflödesanalys En fallstudie på Lammhults Möbel AB
The purpose of this study is to increase the understanding of activities, flows and waste in a company's production process. By performing a value stream analysis, non-value adding activities are identified in a production process and then the suggested improvements that can reduce lead times will be stated. The value-stream mapping identifies the flow of information and the flow of material in a production process and this provides the basis for the identification of non-value adding activities.We conducted the study at Lammhults Möbel AB in Lammhult Sweden, where the Production Flow of Spira-21 has been investigated. This to identify any non-value adding activities that affect the flow negative and consumes time and money in a non-value adding way.A reasonable approach for the project was taken by studying the methodologies and theories. We conducted interviews and site surveys at Lammhults Möbel AB where the flow of information and material in the production process were investigated.
Flödesanalys av plåtsammansättning : Strävan mot Just-In-Time och minskat slöseri
The Volvo Trucks plant in Umeå is a highy complex manufacturing facility where the same production line handles a variety of different models. This require flexible and agile processes with high quality standards. This thesis studies the flow of material through a production line and how Volvo can use their existing manufacturing monitoring system to optimize the flow of materials.The goal with the thesis is to identify eventual problems with the flow of materials and to deliver a few proposals on how the production line can improve its productivity. The theory of LEAN, Just-In-Time and Supply Chain Management serves as the scientific reference to this project. By analyzing the flow of material, performing interviews and observing the processes a few problems are identified.
Opera i Stockholm : Stadsgårdskajen
The report is about efficiency of a current production group where there is no clear Production Flow and there are some buffers between the operations. The efficiency is done with the help of a tool that is calledWork process of flow production which is used by Atlas Copco CTO. The most obviously results are that the lead time drops from 25 hours to 425 minutes and that the balancing loss decreases from 85 % to 8 %. The report focus on decreasing transports, decreasing buffers, more reliability in lead time and quality. And a more stimulating labour content for the workers is another result..
Opera i Stockholm, Stadsgårdskajen
The report is about efficiency of a current production group where there is no clear Production Flow and there are some buffers between the operations. The efficiency is done with the help of a tool that is calledWork process of flow production which is used by Atlas Copco CTO. The most obviously results are that the lead time drops from 25 hours to 425 minutes and that the balancing loss decreases from 85 % to 8 %. The report focus on decreasing transports, decreasing buffers, more reliability in lead time and quality. And a more stimulating labour content for the workers is another result..
En rörig historia : en fallstudie över Secorocs processflöde av DTH-rör
Abstract Title: A messy story ? a case study of Secorocs process flow of DTH-pipes Presentation date: 2010-06-02 Course: Bachelor thesis in businessAuthor: Kristoffer ForsmanAdvisor: Kjell GustafssonKeywords: Management control, process control, lean production, process flow analysisPurpose: The purpose of this bachelor thesis is to develop an overview of the process flow for a specific product, and with the help of this mapping based on a lean production philosophy show possible improvement proposals and how these can lead to a more efficient process flow.Methodology: I have used a case study of Secorocs DTH-pipes and my primary data are gathered through interviews and observations. I have used theoretical framework to establish a process flow analysis. This is to obtain data on process activities and whether they are creating value or not. This leads to a current mapping of the situation in Secoroc on DTH-pipes and then analyzed and suggestions for improvement are developed.Conclusions: That by using the above mentioned mapping of process flow of DTH-pipes, problem areas could be illustrated.
Information ochmaterialflödesförbättrings analys
This examination work is performed at the institution of industrial economy and production at Jonkoping technical university, for JELD-WEN Door Solutions plant in Forserum.Today the focus in the company is on to reduce their inventories binding of capitals as well as inventory of products and that includes to get a good control of the supply and handling of material which is of great importance.JELD-WEN Door Solutions is one of the worlds leading producers of windows and doors and the head-office is located in Oregon, USA.A great number of wooden doors are manufactured by the company in varying of constructions, classifications and performance.The production of the plant in Forserum has a project- and customer focus manufacturing where only internal doors are produced. The overall market they are concentrated on is to different institution such as schools, hospitals etc.The purpose of this work is to investigate possibilities to improvement of material- and production control at JELD-WEN. The report will handle the master production schedule to and from the production divisions within manufacturing industry. Focus will be on the way for information- and material flows from arrival, transport within the company and further on to customers.Further a map of the flow was performed which gave a clearer picture of the connection between the flow of information- and material for the manufacturing process. On the basis of the mapping of the flow, the group discovered that the flow of material had some improvement potential.
Just In Time : Effektivisering av materialflöden med hjälp av principer från Inventory Management och Production Management
AbstractManagement is a field that started getting attention in the beginning of the 20th century by Frederick Taylor. His publication is called the Principles of Scientific Management and is based on the principles of using scientific methods to find the best way of conducting each operation within a production facility. Many of Taylor?s principles may appear obsolete today but the matter of an effective material flow is still highly current. Efficiency is the relationship between the input into an operation and its result.
Förslag till energieffektivisering och energideklarationsunderlag : Munkebergsskolan och Bredängens äldreboende i Luleå
This examination work is performed at the institution of industrial economy and production at Jonkoping technical university, for JELD-WEN Door Solutions plant in Forserum.Today the focus in the company is on to reduce their inventories binding of capitals as well as inventory of products and that includes to get a good control of the supply and handling of material which is of great importance.JELD-WEN Door Solutions is one of the worlds leading producers of windows and doors and the head-office is located in Oregon, USA.A great number of wooden doors are manufactured by the company in varying of constructions, classifications and performance.The production of the plant in Forserum has a project- and customer focus manufacturing where only internal doors are produced. The overall market they are concentrated on is to different institution such as schools, hospitals etc.The purpose of this work is to investigate possibilities to improvement of material- and production control at JELD-WEN. The report will handle the master production schedule to and from the production divisions within manufacturing industry. Focus will be on the way for information- and material flows from arrival, transport within the company and further on to customers.Further a map of the flow was performed which gave a clearer picture of the connection between the flow of information- and material for the manufacturing process. On the basis of the mapping of the flow, the group discovered that the flow of material had some improvement potential.
Flödesoptimering på sjukhuslaboratorium: En praktisk implementering av lean
This study has investigated the possibilities of implementing lean in a division of a hospital in Stockholm. The goal was to reduce the lead time for the patient to get his diagnose by implementing lean in the two Production Flows of this division. In order to accomplish it, a complete map over the value stream has been done. With the help of the value stream map and lean theory a list over the processes in contradiction with lean has been made. Finally propositions to implement lean and by this way reduce the lead times in this stream have been made out.
Betydelsen av flow i bildskapande och pedagogers betydelse för flow : En uppsats inom bildpedagogik om flow och kreativitet och vilka förutsättningar som gynnar flow.
Uppsatsen behandlar ämnet genus och genusframställningen i barnböcker nu, och för 50 år sedan. För att komma fram till ett resultat har två analysmetoder använts, Nikolajevas mimetiska metod samt en semiotisk bildanalysmetod. Resultatet visar att det skett en förändring av genusframställandet i barnböcker de senaste femtio åren och att den största förändringen skedde i mitten på 60-talet..
Utveckling av en ny tillverkningslina
This report contains results of our study at CTC in Ljungby. CTC produces heating products such as boilers, heat pumps and additional products to their heating systems.The purpose of the report is to make a proposal how CTC will supply their new production line for heat pumps with materials. The proposal includes a production layout and a scheme for how to place the material in the production storage.The new production line will produce two different products and both of them have several variants. The line will also have a mixed flow, so the products can be produced in a random order. These conditions demand that the production line has great flexibility and that the material to all the variants can be stored in the production storage.With these conditions as input we made a layout proposal to the company.
Leanorienterad flödesutveckling : av kärntillverkningen på Affärsenhet Cylinder ASSA AB
Business unit Cylinder at ASSA AB in Eskilstuna are having problem with frictions in their production process. Changes are occurring and older products along with machineries are phased out and transferred to low-cost countries. This opens up possibilities to at a larger extend customize physical flows after Production Flows. The authors where given the task to analyze the production and find problem areas to improve and to give suggestion on how Business unit Cylinder can work to optimize their Production Flow.The aim of the thesis work is to come up with suggestions on how to reduce the lead time in production and how the tied up capital can be reduced. In more detail the task included to find problem areas that are counteracting an effective flow, give solutions on new flows for the production of the cylinder core, give suggestions for new stock points for the production and how the production shall be managed and controlled.During the last twelve months ASSA AB has sold over 700 different types of cylinder cores, and the product range is very wide.